COMPAX CFX-R 80 – Screw Compactor
The Compactor with the HIGHEST CAPACITY & POWER available on the market
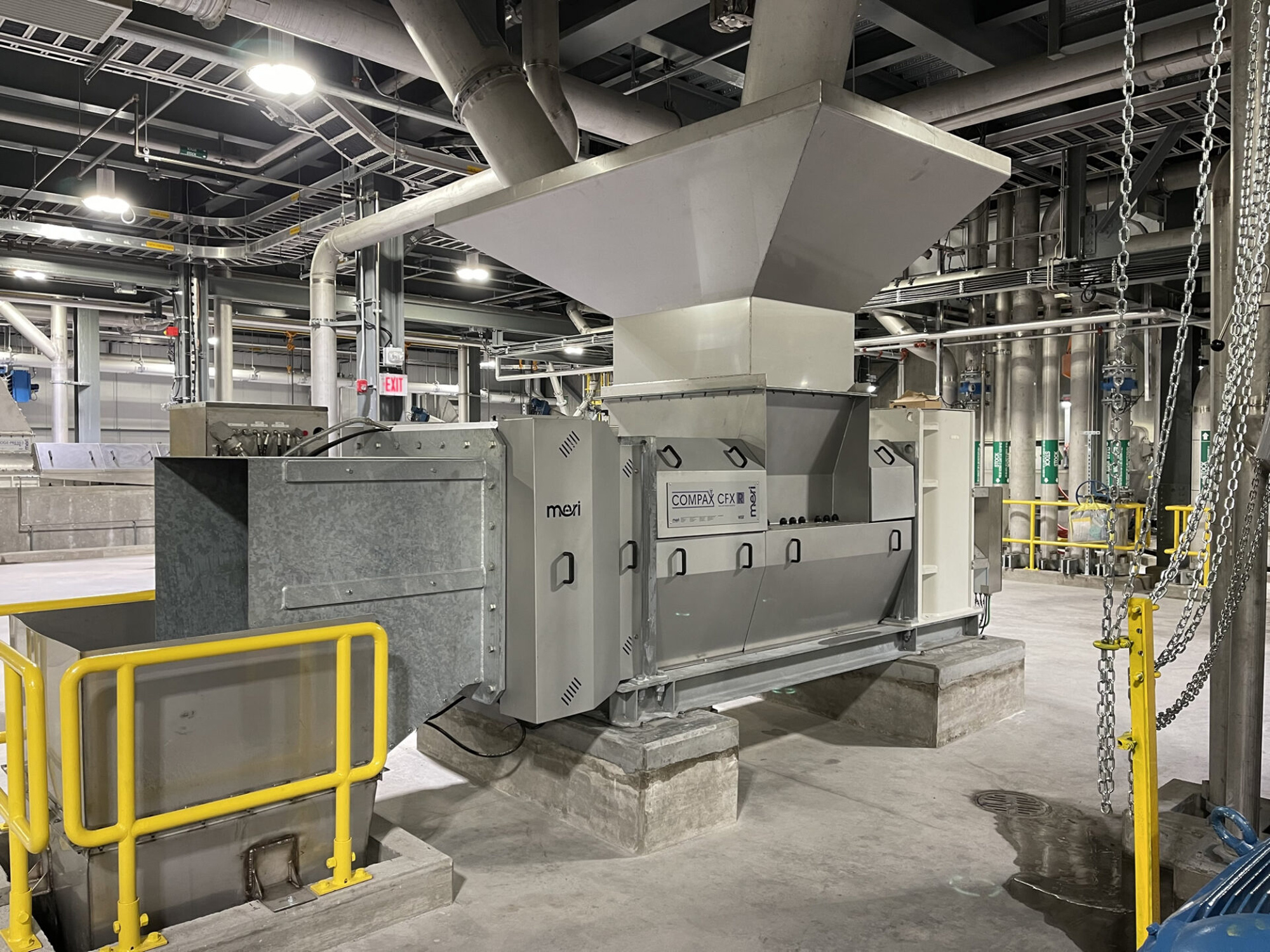
COMPAX CFX-R 80 – Screw Compactor
The Compactor with the HIGHEST CAPACITY & POWER available on the market
Technology
The COMPAX 80 R – Screw Compactor dewaters Lightweight Coarse Rejects from Pulping, Whole Screening and other De-trashing Systems. The slow speed – high torque- rotating Screw presses the Residuals to be dewatered through a Tube Screen Pipe against a Hydraulic operated Twin Flap which generates extreme high counter pressure. Surface water is pressed through the half screens, and collected in the filtrate plan.
The intelligent control & monitoring system allows the COMPAX 80 R to operate with different and/or oscillating Residual Quantities by variating Screw Speed, Press Flap Angle, Torque, Counter Pressure. Depending on the type of material the COMPAX 80 R achieves the 70% TS dryness.
The COMPAX 80 R operates 24/7, up to 10.000 h in a row depending on the Residual characteristics, designed for lowest possible and fast maintenance to reduce cost & downtime.
Features
- Intelligent Machine and Operation Monitoring Control, operation with changing throughputs achieving constant highest pressing results at lowest Energy Consumption
- High Throughput up to 90 BDMT/d, Highest Dryness up to 70% TS,
- Sturdy Purpose Designed Gearbox with Std. SEW Gearmotor for highest Torques, Hydraulic Twin Press Flaps, hinged Press Head and flanged Screw for easy exchange
- Wear Resistant & Low Maintenace Design, highest 24/7 Reliability up to 10.000 h continuous operation
- Slide In-/Out Installation for easy and fast maintenance access
- Exchange, Refurbishment & Service Programs for Screws, Screens & other
Why to buy
- Market Leading Reject & residual Compactor with more then 500 Installations WW
- Next Gen. Intelligent Control optimizes significantly Performance and reduces Wear
- Highest 24/7 Compacting Performance with Lowest Maintenance & Energy Consumption
- Automatic Operation with different throughput achieving highest dryness up to 70% TS
- Capacity up to 90 BDMT/day equal to aprox. 350 MT/d of Wet Reject at ca.25% TS
- Designed for Easy Maintenance and all Wear Part can be refurbished for Maximum Sustainability
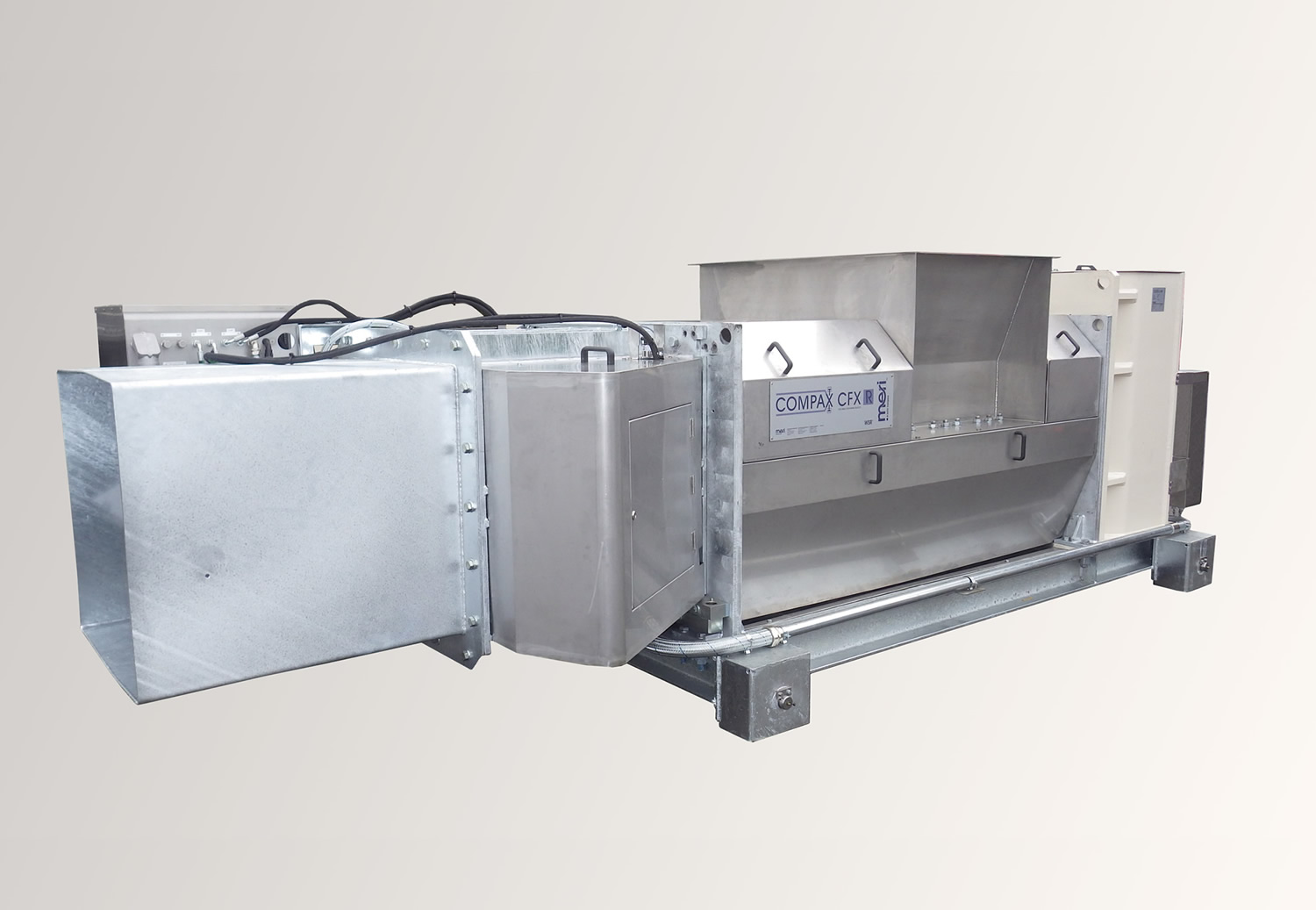
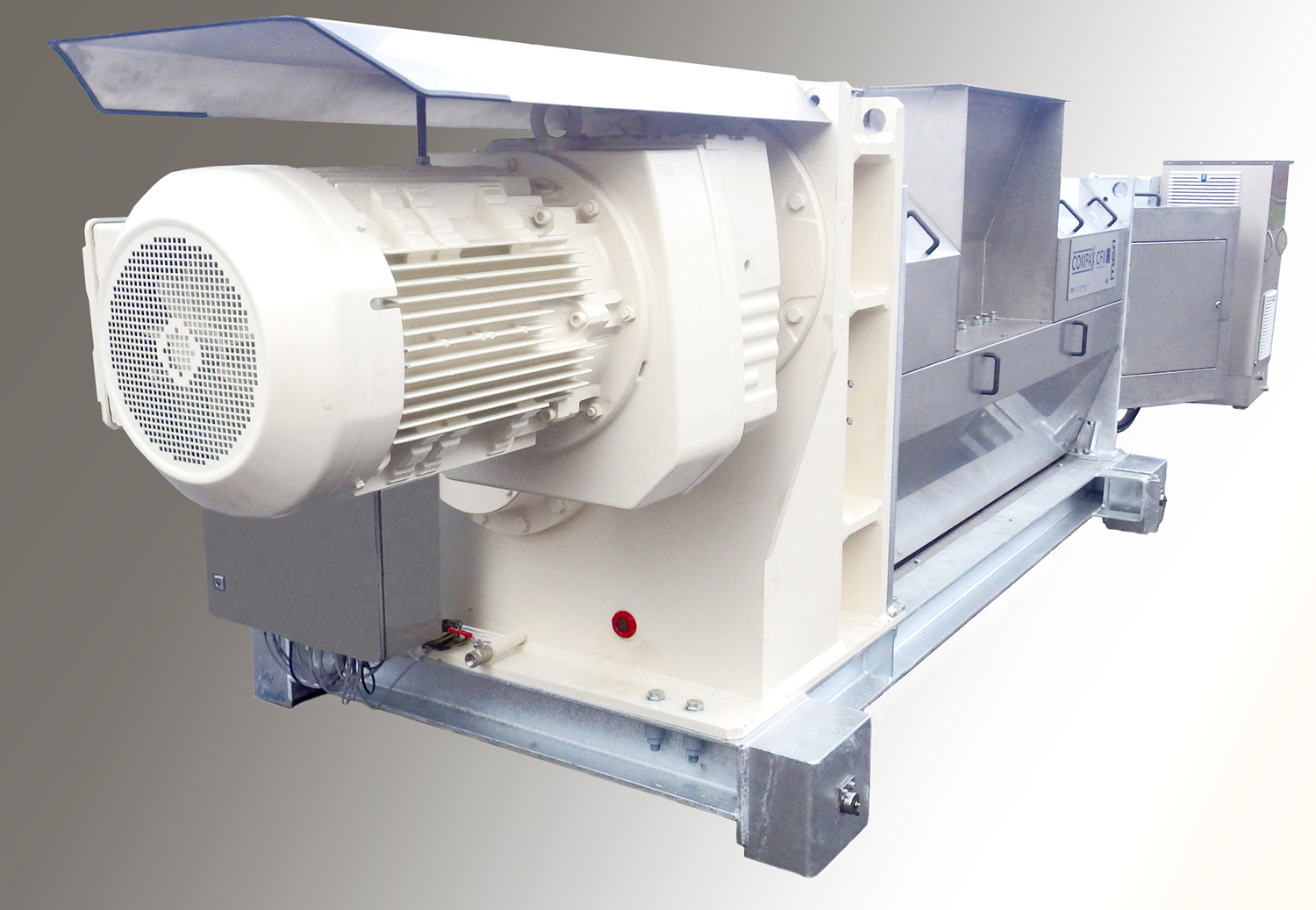
Typical & Proven Process Applications
- Dewatering and Pressing Lightweight Reject from Pulping
- Pressing “Pre- Treated” Lightweight Reject from Drum Pulper
- Dewatering and Pressing Lightweight Reject from De-Trashing Sorting Drum
- Dewatering and Pressing Lightweight Reject from Hole Screening
- Dewatering and Pressing Reject form Hole Screening
- Dewatering and Pressing Reject from Combi Sorter, MODU Screens or similar
See as well the following Products
- COMPAX CFX 60R and CFX 50R
- COMPAX CFX- F 50, 60 for Fibrous Residual Material
- ECOMPAX ECX the Simplified Version
- MBX- Belt Conveyors and MCS- Container Stations a.m.mm
- RSP Sludge and Fiber Residual Screw Press RSP 1150,800, and 650
- Reject Pre-Dewatering with ELEPHANT Disk Thickener
Specifications
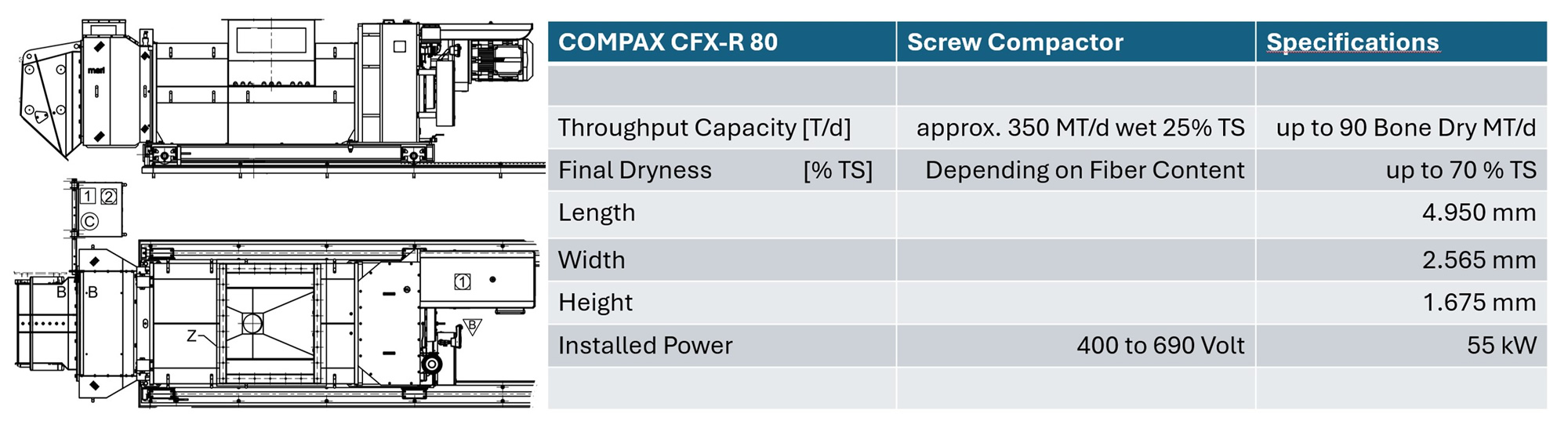